Flux in Soldering: Why It’s Key to Perfect Solder Joints
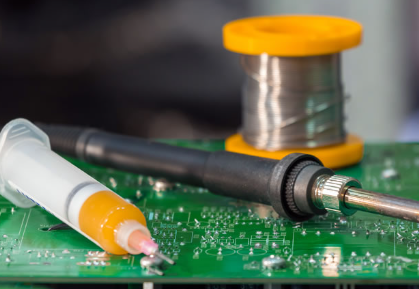
When it comes to soldering, whether you’re assembling a PCB or working on small electronic repairs, flux is one of the most essential materials you’ll need. Though it’s often overlooked, flux plays a crucial role in ensuring strong, reliable solder joints. In this post, we’ll explore what flux is, its different types, and why it’s indispensable in the soldering process.
What is Flux?
Flux is a substance used in the soldering process to facilitate the joining of metals by removing oxides and other contaminants from the surface. The primary purpose of flux is to ensure a clean, strong bond between the solder and the metal parts being joined.
When metals like copper (on PCBs) or component leads are heated, they tend to oxidize, which can prevent proper solder adhesion. This is where flux comes in. By applying flux before soldering, you create an environment where the solder can flow smoothly over the metal, ensuring a solid electrical and mechanical connection.
Why Flux Is So Important
Without flux, soldering would be a difficult and unreliable process. Here’s why flux is so important:
Removes Oxides and Contaminants: When metals oxidize, they form a layer of metal oxide on their surface. This oxide layer prevents the solder from bonding properly, leading to poor connections. Flux chemically cleans the surfaces and helps remove this oxidation, ensuring that the solder bonds directly with the clean metal underneath.
Improves Solder Flow: Flux lowers the surface tension of the solder, making it easier for the molten solder to flow across the joint. This ensures that the solder can form an even, consistent connection between the component leads and the PCB pads, reducing the risk of cold solder joints or weak connections.
Prevents Further Oxidation: While the soldering process takes place, flux helps to prevent further oxidation of the metals. This is especially important for precision work, where any small imperfections can cause significant issues.
Ensures Strong, Reliable Joints: A well-fluxed joint means the solder will flow smoothly and make a proper electrical connection. This not only improves the mechanical strength of the joint but also ensures the long-term reliability of the component.
Different Types of Flux
There are several types of flux used in different soldering applications. Choosing the right flux for your project is crucial to achieving the best results.
1. Rosin Flux
- What It Is: Rosin flux is made from natural tree sap and is the most common type of flux used in electronics.
- Applications: It’s widely used for general-purpose soldering, especially with lead-based solder.
- Characteristics: Rosin flux is typically available in three grades: R (rosin), RA (activated rosin), and RMA (rosin mildly activated). RA flux is more aggressive and is used for cleaning heavily oxidized surfaces, while RMA flux is often used for standard soldering applications.
2. No-Clean Flux
- What It Is: No-clean flux leaves minimal residue after the soldering process, meaning it doesn’t require post-soldering cleaning.
- Applications: Ideal for mass production environments and SMT (surface-mount technology) where cleaning may be challenging or time-consuming.
- Characteristics: No-clean fluxes leave a thin, non-conductive residue that doesn’t affect the performance of the circuit, making them suitable for high-speed manufacturing processes.
3. Water-Soluble Flux
- What It Is: Water-soluble flux can be easily cleaned off with water after the soldering process.
- Applications: It’s used in situations where post-soldering cleaning is required to remove any residue and avoid corrosion.
- Characteristics: It’s often more aggressive in terms of cleaning and is effective at removing contamination. However, it requires thorough washing to ensure no residue is left behind, as it can cause corrosion if not cleaned properly.
4. Organic Acid Flux
- What It Is: Organic acid flux is a type of flux made from organic compounds that are more effective in removing oxidation and contamination.
- Applications: This type of flux is used in situations where the metal surfaces are heavily oxidized or require additional cleaning before soldering.
- Characteristics: While organic acid flux works well for difficult soldering tasks, it’s more corrosive than other types of flux and requires careful cleaning after use.
How to Use Flux Properly
Using flux effectively requires some knowledge and care. Here are a few tips for getting the best results:
Apply the Right Amount of Flux: Too much flux can cause messy residue that’s hard to clean, while too little flux can lead to poor solder joints. Apply flux sparingly to the areas you plan to solder.
Choose the Right Type of Flux: For most electronic applications, rosin-based flux is the go-to option. For automated soldering in high-speed production environments, no-clean flux may be a better choice. If you’re working with heavy oxidation or need to ensure thorough cleaning, water-soluble flux or organic acid flux could be necessary.
Clean After Soldering (If Necessary): Depending on the type of flux used, you may need to clean the PCB after soldering to remove any residual flux. Water-soluble flux can be cleaned with warm water, while rosin flux often requires isopropyl alcohol for removal.
Avoid Overheating: Excessive heat can cause the flux to burn off too quickly, reducing its effectiveness. Always solder at the recommended temperature to allow the flux to work properly.
The Bottom Line: Why Flux Is Essential
Flux is often the unsung hero of the soldering process. It ensures clean, reliable, and strong solder joints by cleaning the metal surfaces, improving solder flow, and preventing oxidation. By understanding the different types of flux and how to use them correctly, you can achieve high-quality soldering results every time.
Whether you’re assembling PCBs in a factory, repairing electronics, or building a custom circuit, flux is a must-have material in your soldering toolkit. It’s one of the keys to ensuring your solder joints are strong, reliable, and capable of supporting the electrical needs of your devices.